Variability in Design for Assembly
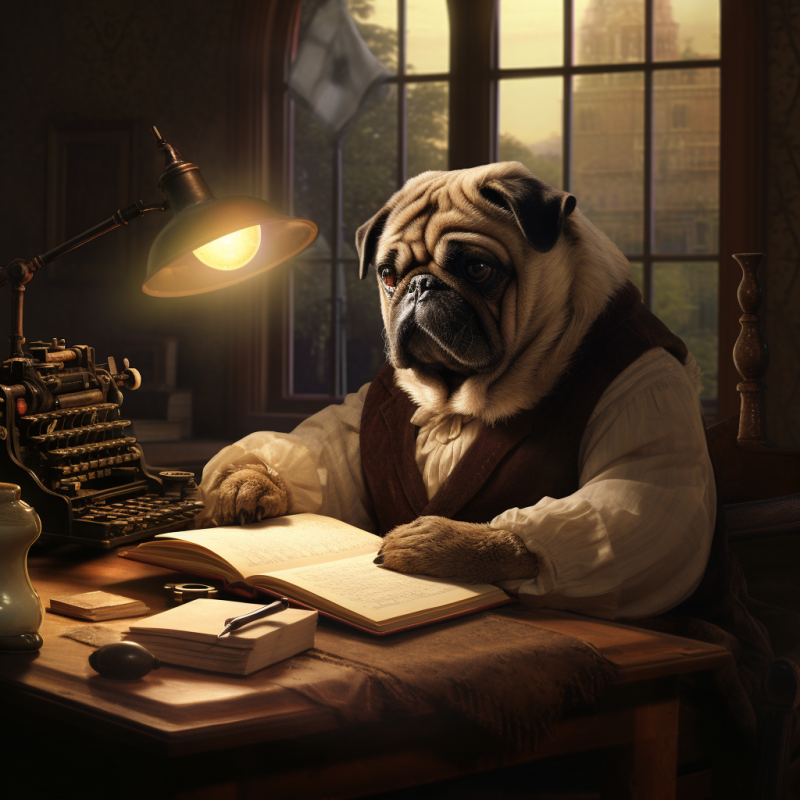
The paper by Namouz, Summers, and Mocko considers the applicability of the Boothroyd and Dewhurst assembly time estimation method as applied to Design for Manufacturing principles [1]. This paper also considers variability sources found within the Boothroyd and Dewhurst estimation method. The paper closes with potential methods of eliminating some variability within the Boothroyd and Dewhurst method.
The Boothroyd and Dewhurst method of time estimation relies on an engineer with some formal training in Design for Manufacturing to answer a series of both empirical and subjective questions regarding the assembly of individual components to create a product [2]. This time estimation method relies on examining both the handling time for each component of a product as well as the insertion time for each component. Each component of the assembly is then examined critically for potential redesign based on minimizing overall assembly time.
Once an engineer has determined that they will perform the Boothroyd and Dewhurst time estimation, they first will break each product down into the individual part assembly steps. Next, the engineer will consider the handling time. The Boothroyd and Dewhurst time estimation system requires that the engineer measure both the radial and longitudinal angular displacement required to position the part in the correct orientation for assembly. The engineer will also consider both the length and thickness of the part. Based on the number of hands required for orientation, the engineer will assign a handling code for the part. Each handling code corresponds to a given handling time. In this way, the engineer successfully estimates the time required to place a part into a product.
After determining the handling time, the engineer must now consider the insertion time. To do this, the engineer considers the relative ease of inserting the part into the product based on tension, torsional resistance, obstructed vision, and several other considerations. These questions tend to have much more subjective answers than the handling questions.
For example, in the Insertion Code determination worksheet, questions are asked regarding the ease of alignment and positioning during assembly. This question does not provide normalized response criteria for the manual dexterity of the worker nor are specifications laid out for what constitutes “easy.” As a result, the engineer may be left questioning what constitutes the criteria for such a response to be valid.
Further questions seek to qualify the amount of resistance found in the assembly process. Resistance can normally be measured in terms of torque required to overcome torsional or longitudinal friction through use of a dynamometer; however, no attempt is made to perform such measurements. Instead, the engineer must consider what they consider to be sufficient resistance to warrant a “yes” or “no” response. As this decision can be demonstrated to be heavily influenced by the individual experiences of the engineer in question, it can be viewed as heavily subjective.
Because of dissatisfaction with the subjectivity found in the insertion time estimate process, Namouz et al. conducted a study to determine the overall effect of subjective questions on the calculation insertion time. Namouz determined that by removing subjective questions, assembly time estimate variability could be reduced from 50% [3] to approximately 15% [1]. This study was conducted using senior mechanical engineering students with minimal training in Design for Manufacturing. The study provided data that was used to synthesize results.
Generally, Namouz provided all reasonable information to ensure the repeatability of the experiment. The primary concern with this study was both a small sample size and a lack of repeated trials. However, as the results match what is typically expected by those familiar with the Boothroyd and Dewhurst method, the study should be considered valid.
References:
[1] Namouz, E., Summers, J., Mocko, G., (2012), “Reasoning: Source of Variability in the Boothroyd and Dewhurst Assembly Time Estimation Method”, ASME International Design Engineering Technical Conferences and Computers and Information in Engineering Conference, Chicago, IL, DETC2012-71075.
[2] Poli, Corrado. (2001). Design for Manufacturing - A Structured Approach. Elsevier. Online version available at: http://app.knovel.com/hotlink/toc/id:kpDMASA001/design-manufacturing/design-manufacturing
[3] Boothroyd G., Dewhurst P., and Knight W. A., 2011, Product Design for Manufacture and Assembly, CRC Press, Boca Raton.
Member discussion