Printed Circuit Board Testing (PCBs Part 4)
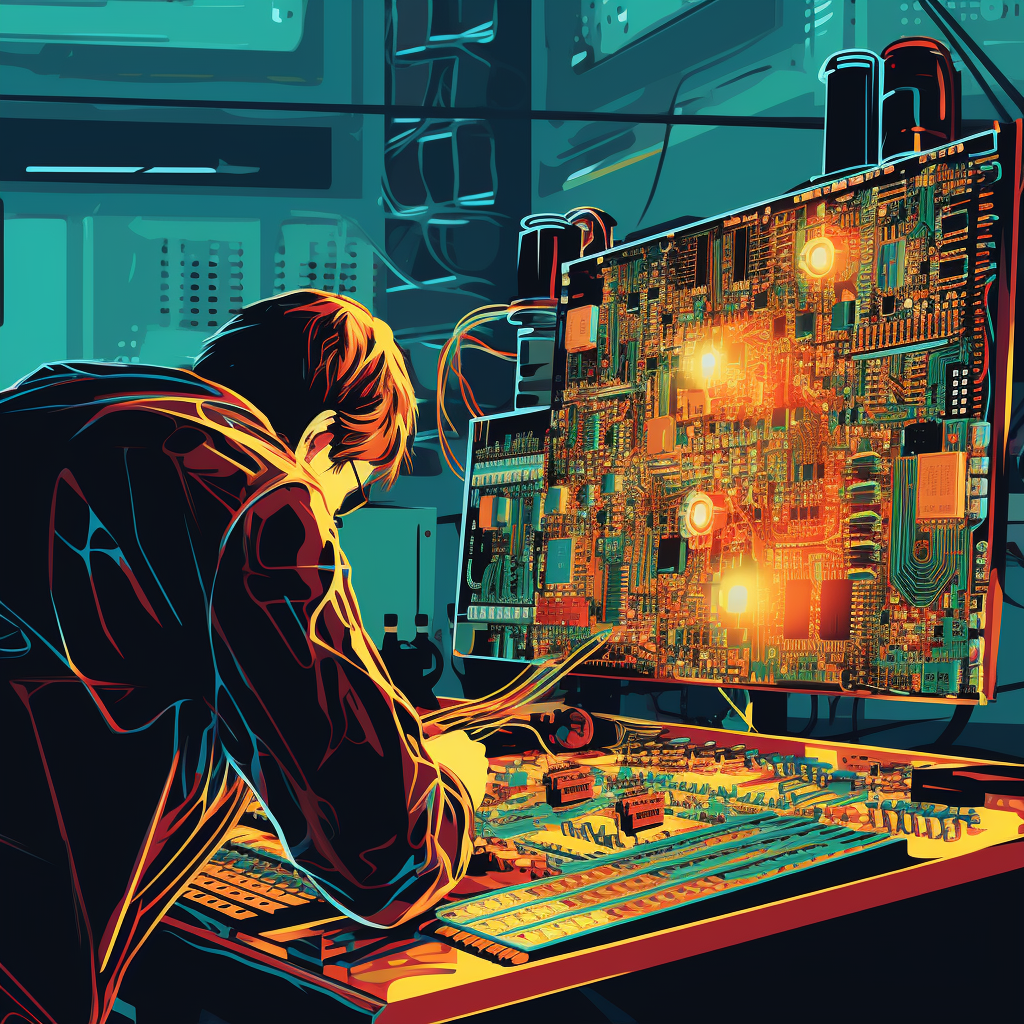
Testing is performed after all assembly actions onboard that PCB have been completed. The PCB is placed in a test fixture and connected appropriately. It is now considered to be a Device Under Test. The test fixture connects to test pads that engineers have purposefully placed on the PCB for this application. Alternatively, intra-layer connection points known as "vias" are also used for the same purpose.
The most common test fixture is a "bed of nails" style tester. This is a custom-made board with numerous connection pins on top of the DUT. Each connection pin is dimensioned to perfectly rest on either a test pad, via, or trace area to be tested. Custom firmware runs on the test fixture to detect incorrect circuit responses. This incorrect response may be due to short circuits, open circuits, incorrect component values, signal degradation, electromagnetic interference, or an incorrectly laid ground plane.
These test fixtures are extremely expensive and may not be warranted for all applications. For example, an inexpensive toy control board may only need a short functional test rather than a full bed-of-nails style test fixture. Alternatively, a PCB expected to undergo numerous revisions would require a custom bed-of-nails test fixture for each revision. Design engineers should consider the associated testing costs with each style. Additionally, additional test points added to a PCB can reduce reliance on custom test fixtures and instead permit the use of individual probe attachments.
After testing, the PCB undergoes assembly to integrate it with the external components it must interface with. Final assembly is the most labor-intensive step, so care should be given to applying standard manufacturing practices. Standard connections should be used whenever possible. Notches and alignment pins should ensure that misalignment or incorrect insertion does not occur.
As the final assembly complexity increases, so too must the build plan instructions. Connectors must be located such that a technician must accomplish the minimum amount of rotation and manipulation possible. Special care must also be taken to ensure that final assembly components do not require special tools to insert them correctly.
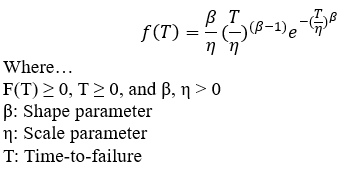
After all assembly and testing operations are completed, the PCB may be subject to a burn-in testing phase. This process allows for early product failures to be found based on the expected reliability distribution. This distribution normally follows a Weibull distribution. Through burn-in, early failures can be detected and rejected. This improves overall net product reliability, as seen by the consumer.
PCB Manufacturing Series:
Part 1: General Design
Part 2: Soldering and Placement
Part 3:Finishing Processes
Part 4: Testing
References:
Cohen, A., 2015, Prototype to Product: A Practical Guide for Getting to Market, O'Reilly, Boston, USA.
Shina, S., 2008, Green Electronics Design and Manufacturing: Implementing Lead-Free and RoHS-Compliant Global Products, McGraw-Hill, New York, USA.
Hubing, T., Hubing, N., 2016, Not-So-Good EMC Design Guidelines,†from http://learnemc.com/not-so-good-emc-design-guidelines
Yates, R., 2014, Probability and Stochastic Processes, Wiley, Danvers, WA, USA.
Member discussion