Printed Circuit Board Manufacturing (PCBs Part 1)
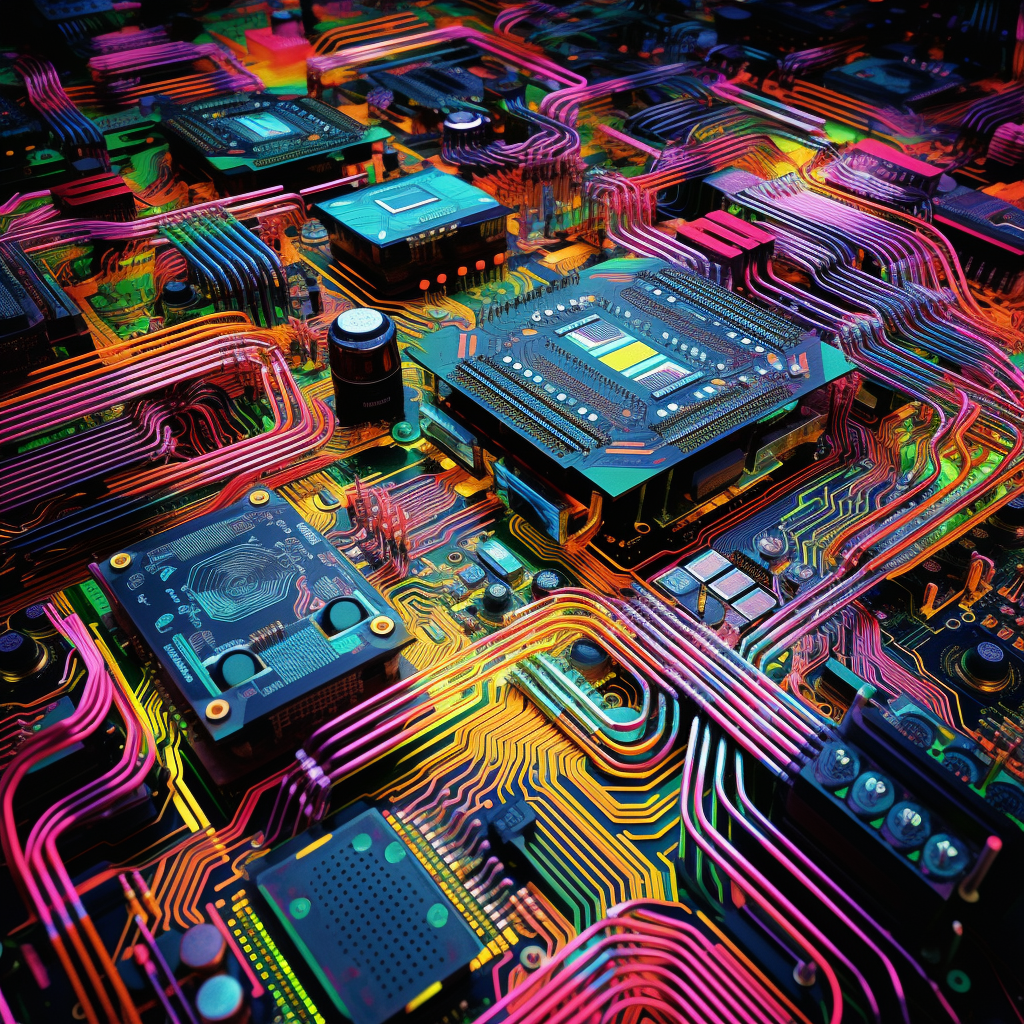
Product development is the art of reducing the number of unexpected surprised to a minimum during the conversion of a novel concept to reality. In electronics design, surprises may manifest in the enthusiastic release of blue smoke or the unobtrusive failure of a particular LED to illuminate during a power-on cycle. Some surprises are born in the foundry when impurities are introduced in a silicon substrate and not discovered until months later during a final acceptance test that reveals an entire circuit board must be scrapped because rework will be cost-prohibitive. By incorporating Design for Manufacturing principles as applied to electronics, design engineers seek to reduce the chance of surprises during production and assembly to produce minimal variability and maximum product test acceptance.
Electronics are manufactured through a series of discrete and well-identified steps. This contrasts the ad-hoc assembly method common in design shops and during initial prototype phases. Typical production runs incorporate hundreds or thousands of individual components assembled to create a circuit board that acts to operate a product. The lack of a single resistor reel can cause all production to be halted until the correct part can be located and loaded into the assembly system.
Electronics assembly follows a well-designed, common flow path regardless of the manufacturer. The first major milestone is before manufacturing ever starts. Components must be identified and available to start production. As electronics components vary wildly in capability from model to model, obsoleted components or single-sourced components must be identified and purchased in bulk, or a line stoppage may occur.
Custom ICs may have several month or year-long lead times. Though it is outside of the purview of most design engineers, several days' worth of component stock should always be maintained on-site. With the global marketplace accelerating the consolidation of chip manufacturers into billion-dollar mega-fab complexes, single-sourced suppliers for particular component lines are becoming more common. Agreements must be in place as early as possible and at the best price. Material costs typically consume up to 90% of a product budget which means that this stage of production is arguably the most vital for a profitable product line.
Prior to PCB assembly, design engineers consider the standard mechanical assembly rules of automated assembly systems. Components must be designed to be orientable by an automated pick-and-place robot with correct spacing for pins, connectors, and sockets. Component placement is normally performed automatically in all but the smallest production runs.
Pick-and-place robots have become so commonplace that hobbyists may own them. Design engineers must pay particular attention to ensure that proper concern is given to the layout of a PCB. Components should be located so that they may be placed by the pick-and-place robot. Components should not be located near the edges as the PCB will have to be cut from the manufacturing panel by a router or other process.
Particular note should be paid to the placement of the ground plane. Ground planes are electrically conductive surfaces that serve as a current return path common to all components on the PCB. Ground planes reduce circuit crosstalk by minimizing inductive coupling between traces. Ground planes may be combined with power planes to serve as a decoupling capacitor for the entire board. Engineers should be cognizant of floating metal present on the PCB and try to ground heatsinks to the ground plane whenever necessary. However, this rule does not always apply to all situations, as insufficient grounding may be worse than no grounding.
PCB Manufacturing Series:
Part 1: General Design
Part 2: Soldering and Placement
Part 3:Finishing Processes
Part 4: Testing
References:
Cohen, A., 2015, Prototype to Product: A Practical Guide for Getting to Market, O'Reilly, Boston, USA.
Shina, S., 2008, Green Electronics Design and Manufacturing: Implementing Lead-Free and RoHS-Compliant Global Products, McGraw-Hill, New York, USA.
Hubing, T., Hubing, N., 2016, Not-So-Good EMC Design Guidelines,†from http://learnemc.com/not-so-good-emc-design-guidelines
Yates, R., 2014, Probability and Stochastic Processes, Wiley, Danvers, WA, USA.
Member discussion