Laser Metal Deposition for 3d Printing
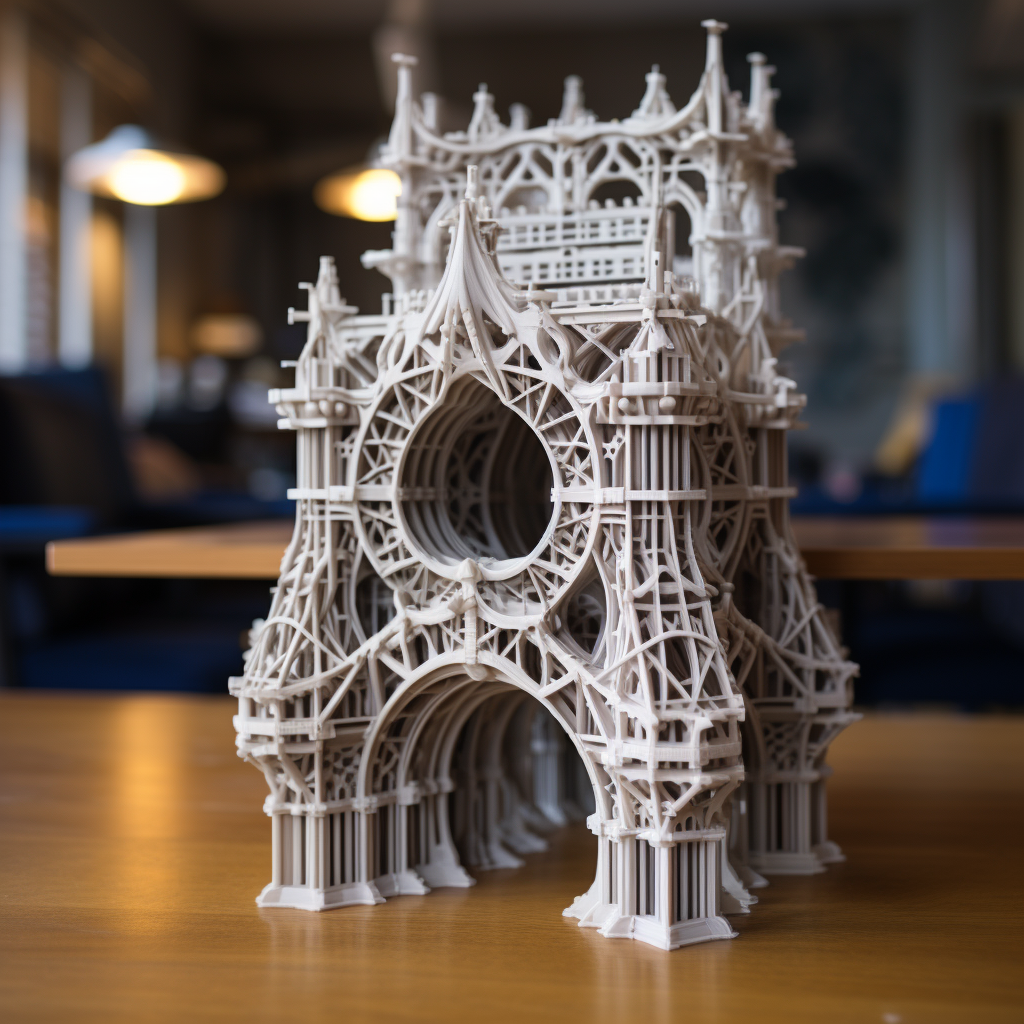
In some applications, high-precision parts must be produced with minimal manufacturing time. Parts that would traditionally be cast or forged are instead produced via an additive manufacturing process known as laser metal deposition. In this AM process, a semi-fixed laser is moved along the x-axis above a moving print bed while metal powder is fed through a hopper directly in-line with the laser beam. This works like some polymer extrusion 3d printers except with the axis of movement reversed between the print bed and the deposition system.
LMD has advantages over traditional manufacturing processes in that extremely precise tolerances may be maintained despite a relatively high production rate. Multi-axis laser 3d printers allow for part production that would otherwise require complex rafting and structural supports. Due to the versatile nature of laser metal deposition, repairing damaged components has become a common application for this technology.
Several patented laser metal deposition systems exist. The closed-loop feedback control system patented by Mazumder and Voelkel allows for noncontact surface contour measurement, which is fed back into the control circuitry of the laser. This allows for immediate correction when dimensional accuracy is at risk due to improper melt pool formation [1][2].
Similar to Mazumder and Voelkel's closed-loop feedback system is the integration of feedforward and feedback systems to provide real-time error anticipation and correction. These types of systems may utilize fuzzy logic and neural networks to correct errors before they happen. For example, sharp corners may be improved by reducing the bead thickness as the edge of the corner is approached. As the laser approaches the edge of the workpiece, a complex series of accelerations and decelerations may occur. To compensate for this while maintaining proper bead size, automatic laser power reduction may be enforced by the sensing system [3].
Hammeke has patented a system allowing equal metal deposition in any direction. This system utilizes a coaxial nozzle arrangement with a nozzle that blows in inert gas during the melting process. This inert gas assists in displacing oxygen molecules to prevent oxidation while promoting ideal powder delivery to the deposition site. Through the use of this system, more complex geometries are possible to be created by the laser metal deposition process [4].
Radiometric feedback is an area of research in laser powder deposition technology. With proper knowledge of the emittance of the metal powder in question, it is possible to design a system that provides accurate information on the material composition, microstructure, chemical contamination level, and surface finish of the workpiece as it is being created. This level of information may be used to calculate the material properties of the workpiece before it has been completed. If residual stresses or thermal performance are unacceptable, the part may be rejected immediately to prevent material wastage [5].
Another area of research in expanding laser deposition technology is in hard-facing and cladding creation. Hardfacing is the process by which a harder material is attached to a softer material. In this case, laser deposition adds protective layers to worn or damaged parts. Adding cladding to finished parts is another way that laser deposition technology is being used. If a finished part fails to achieve tolerances due to being oversized, it may be ground down to size if it is too large. Now, using laser deposition technology, undersized parts may have metal cladding added through laser deposition to meet design tolerances for minimal sizing [6].
One of the more unique applications of laser metal deposition technology is the layering of dissimilar materials. Each layer of a particular part may utilize different alloy powders simultaneously to produce a result with a particular shear strength, Young's moduli, or thermal transfer characteristics. Additionally, laser characteristics may be altered during part creation to achieve particular phase transition points in different parts of an otherwise homogenous material. This allows the design engineer to determine grain structure in discrete areas of a given part or product.
Much of the ongoing research in the field of laser metal deposition involves the integration of Aluminum alloys into common usage. These alloys are particularly difficult to work with due to their high laser reflectivity. As a result, achieving a satisfactory melt is difficult. Additionally, special precautions must be taken to prevent equipment damage due to the reflection of the laser. Once ideal laser parameters are established, research will move into reducing material porosity and residual stresses from the manufacturing process [6].
Laser-based additive manufacturing can be categorized into three primary categories of direct metal laser sintering, selective laser melting, and laser metal deposition. Each method carries with it advantages and disadvantages. Current research has resulted in ideal parameters and methods for fabricating particular materials.
References:
[1] Mazumder, J., Voelkel, D., 1995, "Method and Apparatus for Noncontact Surface Contour Measurement," US Patent Number 5446549.
[2] Mazumder, J., Morgan, D., Skszek, T., Lowney, M., 2010, "Direct Metal Deposition Apparatus Utilizing Rapid-Response Diode Laser Source," US Patent Number 7764022.
[3] Srivatsan, T., Sudarshan, T., 2016, Additive Manufacturing: Innovations, Advances, and Applications, CRC Press, Boca Raton, FL, USA.
[4] Hammeke, A., 1988, "Laser Spray Nozzle and Method," US Patent number 4724299.
[5] Gebhardt, A., Schmidt, F., Hotter, J., Sokalla, W., Sokalla, P., 2010, "Additive Manufacturing by Selective Laser Melting: The Realizer Desktop Machine and Its Application for the Dental Industry," Physics Procedia 5, 543-549.
[6] Gu D., Meiners, W., Wissenbach, K., 2012, "Laser Additive Manufacturing of Metallic Components: Materials, Processes, and Mechanisms," International Materials Reviews, 57:3, 133-164.
Member discussion