How are Injection Molding and Die Casting Related?
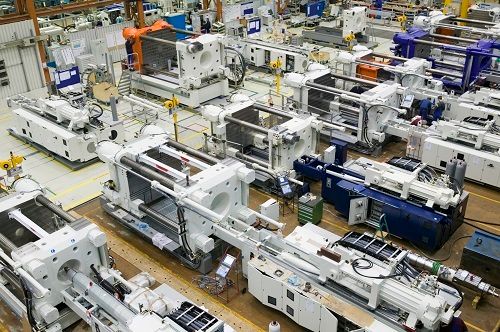
Injection molding and die casting are similar manufacturing processes that produce parts for product assemblies. While these processes follow a similar flow, there are some differences you should consider.
In injection molding, a softened plastic material is injected into a mold, heated, and allowed to cool. This is different from die casting in that die casting uses a fully liquid metal. The closest analog to this in metal manufacturing would be drop-forging. Even still, drop forging will cause significant changes to the metal in question due to changes in the atomic structure. As there is phase transition in the metal, there is also concern regarding recrystallization of the metal. This usually much less of a concern in plastic goods. However, some plastics such as Bakelite do require special processes to ensure phase transition occurs correctly.
After the mold has been injected with either softened plastic or liquid metal, cooling must occur. The same general guidelines for designing parts to accommodate cooling apply in both injection molding and die casting. Thin walls tend to perform better than thick walls. Varying thicknesses can lead to uneven cooling and result in an undesirable product.
Both systems of part manufacturing have a risk of porosity problems. Similarly, there also exists a risk of sunken areas in both injection molding and die casting. Die casting reduces this risk by use of vacuum pumps. This is also solved in the same way in injection molding.
Both injection molding and die casting are at risk of using more complicated molds when undercuts are frequently used. Both systems also have some difficulty with sharp corners. Both systems make use of fillets and rounds to improve overall product quality. Both systems also make use of draft angles to improve the ability to remove the product from the mold. Both systems make use of ejector pin assemblies to ensure the product can be removed from the mold.
Neither processes tend to require significant post-processing beyond removal of flash and sprues. Both processes do have concerns regarding surface finishes. However, only die casting offers significant opportunity to correct surface finish imperfections in post-processing. This can be accomplished by grinding, buffing, or any other similar process to smooth out surface imperfections. The same post-processing options are often not available in many plastics applications.
Ultimately, the same principles can generally be applied to injection molding and die casting. While the processes have some differences, the underlying physical processes are similar enough that general rules still apply. An individual that is experienced in either plastics or metal die manufacturing will find that much of their experience is easily translatable.
Member discussion