Historical Survey of Engineering Design
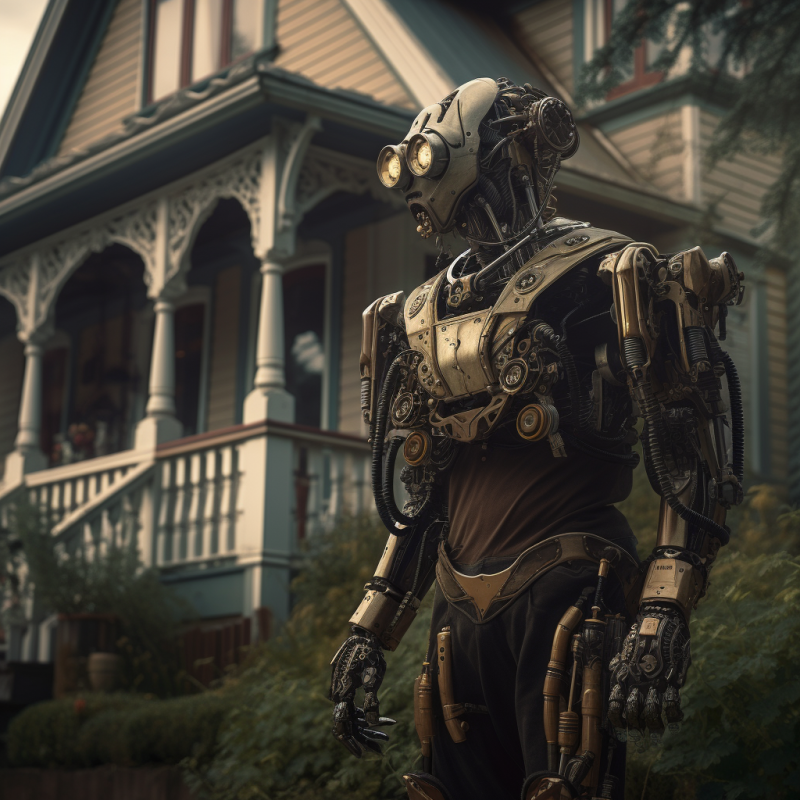
General Comments on Publications and Research
The reviews under consideration provides insight into the value of researching current publications. Researching current publications can provide the ability to increase knowledge in a specific subject, or provide the foundation for extending research and knowledge. Most research and publications focus on a particular aspect of a topic, with the goal of identifying conclusions that are currently unknown or ambiguous. The research provides focused experimentation or study of this aspect, often leaving other parameters open to further research. For example, research studying surface finish of particular coatings would leave subsequent research topics open for experimentation, such as coating adhesion on different materials. There is infinite possibility for innovation, and research provides the path on which to strategically make improvements. Thus, research provides insight into advancement, but also identifies aspects that require additional research and study.
Publications should read with proper context in mind. It is important to understand the historical and topical context of a paper. For example, this paper was written in 1989, so many points of discussion seem outdated in 2023. It is important to understand this when beginning to read the publication, as perspective will change and lessons learned from the publication will also be affected. In this paper, the important lesson learned was the value of gathering various studies into a focused overview with historical perspective on how the gaps were filled. I believe a firm grasp of history is an important foundation to help shape future advancement.
The topical context of the paper provides the ability to extract useful information. If I found a graphical design publication and read it expecting to learn about engineering design, I will either waste my time or have a flawed understanding of the material. This highlights the importance of clarity within the paper to effectively communicate the scope and purpose to the reader audience.
Having understood the proper context of a publication, the paper should then be read critically. This requires not only reading to learn from the paper, but also reading to question the content and conclusions for accuracy and logic. The references provide additional resource to ensure the content has been accurately represented. For this reason, the current publication states that errors of commission (misrepresentation) and omission (inadequate representation) may be committed by authors [1]. Thus, it is important to critically evaluate the content of the publication.
Purpose of the Study
The review performed by Finger and Dixon [1] is to investigate research topics within mechanical engineering design. The review was published in 1989, so it must be evaluated in this historical context. The review illustrates not only how mechanical engineering design has developed, but also how to effectively study current research publications and to identify gaps. The review intends to distribute knowledge and an overview of current research in engineering design [1]. The practical goal of the review is to equip engineers to better understand design tools and to improve design activities [1].
Scope of Paper
The authors identify 6 topics within mechanical engineering design methods: 1) descriptive models, 2) prescriptive models, 3) computer based design models, 4) languages and domains of design, 5) analytical design models, 6) design for product life cycle [1]. The authors identify the computer application discussion will not include specific software, but rather the topical aspects of research [1].
The paper was based on research within the United States, which was performed before 1990. The authors identify engineering design as an emerging and developing field, with opportunity to explore new research [1]. One of the authors (Dixon) produced a paper discussing the goal of scientific theory within engineering design research [2]. The authors consider questions that seek to identify opportunities for automation in design, and argue that the existing uncertainty indicates a lack of understanding within the entire subject of engineering design [1].
Descriptive Model
The descriptive model of design attempts to understand and describe the methods used by engineers to design. The authors make the distinction between methods (such as brainstorming) and the systematic organization of processes within design [1]. The research under consideration mostly includes design during the preliminary design stage [1]. The studies are referred to as “protocol studies” and include comparison of design activities within and outside of the comfort zone of designers [1]. The authors identify the lack of research on design behaviors at different stages of design and how they may differ [1]. Other research observes designer behavior and concludes that design methods and processes are repeated in progressively more detailed levels within each design stage [1].
A challenge within studying design thinking and reasoning is the limited ability to capture reasoning that occurs within the designer’s thoughts, and whose specific steps cannot easily be transferred to paper [1]. Research investigates the aspects of familiar and unfamiliar design techniques, with the goal of capturing procedures that can be translated into automated efficiency tools or automated computer design program [1]. One challenge with design is that design should be open to a wide solution space, yet researchers observe that many designers prefer to adapt solutions rather than to explore new options [1].
The effort to translate human engineering design processes into computer based models is referred to as cognitive models. As discussed, the challenge is to capture the human process and translate into computer algorithms. Research concludes that the cognitive model is distant from the intricacies of human behavior, and cognitive model is limited to symbolic representation as opposed to mathematic representation [1].
While the authors do not indicate that full automation of the design process is possible, they acknowledge that research concedes that improved computer based design tools are required and should be based on descriptive models of human engineering design activities [1].
Reflection - Descriptive Model
Many of the observations on design behaviors are correct, in my opinion. The challenge with formulating a generic descriptive model is that not all design problems are the same. Also, new solutions require deviation from traditional approaches. Computer based tools will be limited (in near future at least) to the ability in which they are created. In other words, it will be an extremely difficult task to create an independent artificial intelligence system that can surpass the design ingenuity of humans. Without that ability, computer based tools will only be as good as the programmer and the flexibility within the algorithm. This will restrict not only the ability to match human design, but also the ability extend into novel design. The challenge of that goal does not mean research should not pursue it, but rather this should be taken into account and computer based tools should be built around user friendly interface to be directed by a design engineer.
I agree with statements that most designers tend to adopt and implement existing designs (or adaptations) in preference to novel designs. This could be a result of engineering education in engineering science, where engineers must work from a general theory, including many assumptions, then eliminate assumptions to improve their answer as necessary. This process can be emulated during design activities where the engineer attempts to improve a single concept through iterative attempts to formulate and solve the problem. Another consideration is that it makes sense to use available and proven design, rather than to try to “re-invent the wheel” with every design. Of course, novel designs can be quite useful and the search for them must be pursued when the design problem and potential benefit merit the investment of resources.
Prescriptive Model
The authors acknowledge a range of disagreement within the prescriptive model of engineering design. The prescriptive model is related to how the design process should be performed. The range of opinions include the unorganized “creative” approach, organized “systematic” approach, and the approach that there should be no prescribed method [1]. The assumption in having a prescriptive process is that adherence to a process will result in improved design [1].
The realm of design types are classified similarly to Pahl and Beitz [3], including novel design, adaptive design, and variant design. The overall “canonical” design process described in the review [1] is similar to the stages presented by Pahl and Beitz [3]. The authors present 3 stages of thought: divergence, transformation, and convergence [1]. The transformation aspect is a new term, but includes considerations of refining the problem and requirements. An important aspect of human design approach is the background and experience of the designer [1]. The authors provide multiple resources to illustrate the conflicting views on design, as some believe that designers will not follow a prescribed process because a structured approach is unrealistic and unrepresentative of the design process [1].
The authors focus on the selection process within morphological analysis. Important considerations and assumptions within the morphological approach include division of the problem, relationships of sub-problems, solution matrix representation and evaluation of solutions, and a methodical approach to combine solutions [1]. This approach has been presented in Pahl and Beitz [3], as well as discussed in class due to its ability to organize solutions and combine compatible sub-solutions.
The authors proceed to describe axiomatic approaches, which emphasize characteristics that a design should exhibit, as opposed to an itemized procedure [1]. The axiomatic design approach provides the goal of designing with independent functional requirements through simple solutions [1]. The authors distinguish functional independence from physical independence, as a single part could provide solution to multiple functional requirements [1]. Another axiom is the prevention of quality loss through design. The Taguchi method employs statistical methods to evaluate the quality of design through later stages of product life cycle (manufacturing and product use) [1].
Reflection – Prescriptive Model
The variety of opinions on design approaches and methodologies provide plenty of room for discussion. Previous assignment discussions of Pahl and Beitz have considered the flexibility and challenges using a systematic approach. When applying a systematic and structured approach, it is important to remember that the process does not create a good design by itself. The important takeaway of the systematic approach is that the structure is intended to encourage engineering design activities and creativity. Following the procedure for the sake of procedure adherence misses the point of the process.
The conclusion that most designers do not follow the canonical process [1] appears to be indicative of the workforce (from experience). In most cases, if people are not required to follow a process (or held accountable), they will not do so. From experience, you can put together a list of requirements, but it may only be useful to you because others will not critically evaluate it. Actual adherence to a design process is probably first linked to the culture of the work environment, then linked to individual training and experience. With development in engineering education, it is likely that the use of a systematic approach to design has increased, compared to research findings in 1989.
The authors note that (at the time of the publication) there are no current research efforts to link prescribed methods to design success. There is likely data to support this conclusion in 2016, as the field of engineering design has developed. Within the scope of engineering design education, experience and research has indicated that inadequate education in design results in a deficient industry [4, 5].
In the 1970s, ABET sought to address this shortcoming of engineering education with the goal of improving industry performance [4]. In order to close this gap, it was recognized that engineers must understand how to take open ended problems and generate solutions while implementing sound decision making abilities [4]. Whether this justifies a particular systematic approach over another is unclear, but it requires some form of structured approach to define and problem and to select an appropriate solution. Recent studies may be researched to evaluate comparison of engineering design approaches, such as that performed by Maier and Fadel [6].
The authors [1] do note the importance of this research, as the potential to increase the scope of design solutions can improve the final design selection. It is generally accepted that improvement of the initial design significantly improves the final outcome and determines the majority of the product cost. Specifically, the conceptual phase of design determines 70% of the manufacturing costs of the product [7], so DFM research has also evaluated the importance of sound design practices.
The additional consideration of “transformation” provides an interesting take on the design process that helps emphasize the aspect of iterative steps and continual open-minded approach to design. This is an important part of design that could be emphasized more within the method presented by Pahl and Beitz.
The authors of this paper acknowledge the consideration of the background and training of designers and the impact on design approaches. This is an important aspect to the flexibility aspect of the design process. As Pahl and Beitz note [3], design tools should never be imposed on a designer, as the designer should be free to select tools and methods suitable to preference or the particular design problem. The criticism of systematic approach is not necessarily incorrect when a design procedure is enforced with the assumption that it will produce a good design. A balanced approached should be taken to use the systematic approach and methods to best facilitate the design process.
The axiom of functional independence is a good aspect of design, but was not elaborated in detail (at least pragmatically). As discussed in class, the independence of functional requirements helps to clearly identify sub-solutions that do not overlap or contradict each other. The authors identify the challenge with axiomatic design, related to quantifying and understanding quality loss over the lifespan of the product [1]. This type of work has likely expanded since the publication of this paper, as research methods develop and explore design for manufacture and design for excellence.
This section of the paper was likely relevant at the time. The general discussion of design theory still relevant. As the paper is substantially dated, updated research is needed. All of the sections on Computer Aided Design are significantly outdated as feature based modeling is the most common method of design. However, this section still provides an excellent historical narrative to draw from.
Analysis in Design
Once a design has undergone the previously discussed stages of development, Finger and Dixon write that design analysis should be performed [1]. Without analysis to back the design, the results of the product may be substandard. In order to qualify a design, engineers must perform calculations and experiments that generate data on topics such as moment arms, fatigue, stress and strain, deflection, material concerns, and thermal performance. Without this data, designs lack data certifying the product to perform to specification.
One historical development in design analysis was performed by researchers at Brigham Young University. BYU produced a knowledge system which allowed for optimization of provided data for analysis. This program allowed designers to import data from existing software. Design problems could be inputted and defined accordingly. The program then output results as applied to potential design improvements stored in the database [2]. This primitive expert system allowed for rapid enumeration of options constrained to known problem solutions.
Another historical expert system developed around the same timeframe was SYMON. SYMON was created by Agogino et al. to perform monotonicity analysis in order to qualify existing constraints and to understand their impact on the design process [8]. SYMON (Symbolic MONotonicity analyzer) was combined with SYMFUNE (SYMbolic FUNctional Evaluator) to perform the Karush-Kuhn-Tucker optimization algorithm for design problems. This artificial intelligence system provided non-numerical analysis was used to establish general trends as opposed to parametrized results. This is in contrast to numerical analysis systems such as ANSYS and NASTRAN.
Where SYMON performs monotonic analysis, SYMFUNE performs functional evaluations. These calculations were performed using a custom FORTRAN program called FORTRANIZER to translate encoded data into the SYMFUNE native data structure. SYMFUNE was intended to act as a design aid for the engineer to perform optimal design. Unfortunately, design complexity causes an exponential increase in algorithm runtimes.
As non-numeric optimization schemes are less likely to face unrealistic runtime requirements, substantial research in early optimization systems was focused on non-numeric system implementation. SYMON/SYMFUNE would eventually perform symbolic optimization to establish a list of acceptable constraint values held within a domain of optimality based on running the Karush-Kuhn Tucker equations. For example, design studies could be performed which allowed a design engineer to determine the optimal range of cross-sectional areas of a part while still maintaining an acceptable cyclical stress safety factor.
Development of other design optimization procedures led to an increase in the use of finite element analysis. Finite element analysis is the process by which perturbations in a system are approximated by modeling small sections of the system as geometric shapes. The impact of each geometric nodal section on other sections is analyzed across the system as a whole in order to establish a generalized system response.
Finite element analysis programs such as NASTRAN and PATRAN were developed to easily generate and analyze finite element meshes. Early predecessors to NASTRAN and PATRAN were created in order to analyze basic design problems such as cantilever beams and thin-walled plates. As a result of development in the field, modern programs allow for stress/strain relationships, acoustics, thermal transients, and electromagnetic interference to be easily modeled to validate calculations.
As technology has progressed since the writing of this paper, so too have the analysis techniques. Programs once used exclusively in experimental academia have become built-in features on low to mid-ranged programs. Most CAD programs now include some design optimization and design study features. As a result, engineers are able to make regular use of optimization algorithms to achieve cost-effective solutions.
Reflection – Analysis in Design
This section provided an excellent overview of the history of design optimization techniques. Although the material was dated, Finger and Dixon elaborate on various early solutions to the problem of establishing design studies as a formalized process. Although the systems discussed in the article are generally no longer in use, successor programs are available that make use of the knowledge gained through expert system design.
As this article was substantially dated, the majority of the value lies in providing a historical perspective for the state of modern engineering. Seeing the development of expert systems through the lens of those that first envisioned them provides great value in appreciating the many forks and dead-ends inherent in the process.
Design for X
Design for X is a set of rules governing design in order to accomplish an improved ability to perform the subject of the design rule. Design for Manufacturing allows for an improved ability to fabricate parts. Design for Assembly provides for methods by which assembly steps are removed or reduced in complexity. Design for Analysis results in products which are optimized for design studies or other analysis techniques.
As economic incentives for producing low cost parts rise amidst competition for the best value products, companies have long sought to decrease manufacturing costs. One method Finger and Dixon write about to achieve this is known as concurrent design. Concurrent design is the process by which all product lifecycle stakeholders from engineering to marketing are involved in the design process. This ensures that each stage of the design process has inputs from interested parties. As conflicts are discovered earlier in the design process, less effort is required to conduct redesign actions.
Another important aspect of concurrent design is the concurrent design of individual parts that make up the product. Though this may require a larger manpower commitment, it allows for part compatibility to be assured. Redesign due to compatibility issues adds an increasing cost the later that the incompatibility issue is discovered. Because of this, the increased initial manpower cost associated with concurrent design frequently pays for itself.
Design for Manufacturing is a process created largely by Boothroyd and Dewhurst. This process was later formalized as a spreadsheet driven scoring process [4]. This scoring process encompasses handling requirements, rotation requirements, insertion times, tool assistance requirements, and many other characteristics. Additionally, research in Design for Manufacturing principles has resulted in the creation of hundreds of rules for design by researchers such as Bralla [11]. Through DFM scoring and incorporation of design rules, parts may be designed or redesigned to produce optimal end products.
Finger and Dixon also discuss tolerances. From the perspective of Design for Manufacturing, tolerances increase part complexity according to Poli [10]. Additionally, poor consideration of tolerance stacking may result in a failed component assembly. These considerations must be considered by design engineers at the earliest stage of the design embodiment as possible. As the design matures, the cost of redesign increases.
Reflection – Design for X
There is no doubt that Design for Assembly, Design for Manufacturing, and Design for Analysis play a vital role in optimizing a product for optimal manufacturability and cost avoidance. This section provided an overview of early Design for Manufacturing development. Additionally, some consideration was made for other DFX procedures.
As this was an early writing on the topic of Design for X, it must be reviewed in context of the limitations on the authors of the time. Substantial detail could be said to be missing when viewed through the perspective of a trained Design for X practitioner. However, as these details were missing at the time of the writing, the authors should not be considered at fault.
This material is useful in that it provides an excellent historical context for the development of modern manufacturing design processes. Although much of the information provided is of limited use when compared to modern material, understanding the early-state of DFX provides a heightened appreciation for the current-state system. Additionally, it may be useful to use this knowledge to forecast future-state DFX
REFERENCES
[1] Finger, S. and Dixon, J. R., 1989, "A review of research in mechanical engineering design. Part II: Representations, analysis, and design for the life cycle," Research in Engineering Design, 1(2) pp. 121-137.
[2] Dixon, J. R., 1988, “On Research Methodology Towards A Scientific Theory of Engineering Design.” Artificial Intelligence for Engineering, Design, Analysis and Manufacturing (AI-EDAM), Vol. 1, No. 3.
[3] Pahl, G., Beitz, W., Feldusen, J., and Grote, K. H., 2007, Engineering Design: A Systematic Approach, 3rd edition ed. Springer-Verlag. Berlin.
[4] Nicolai, L. M., 1998, “Viewpoint: An Industry View of Engineering Design Education.” TEMPUS Publications.
[5] National Research Council, 1991, “Improving Engineering Design, Designing for Competitive Advantage.” Washington, DC.
[6] Maier, J.R. and Fadel, G.M., 2005, “A Case Study Contrasting German Systematic Engineering Design With Affordance Based Design.” International Design Engineering Technical Conferences and Computers and Information in Engineering Conference, ASME.
[7] Poli, C, 2001, “Design for Manufacturing : A Structured Approach.” Burlington, US: Butterworth-Heinemann, ProQuest ebrary. Web. 10 September 2016, p. 9.
[8] Bailing, R., Parkinson, A. and Free, J., 1982, "OPTDES. BYU: An Interactive Optimization Package with 2DI3D Graphics," Langley Research Center Recent Experiences in Multidisciplinary Analysis and Optimization, Part 2; pg. 12
[9] Agogino, A.M. and Almgren, A.S., "Techniques for Integrating Qualitative Reasoning and Symbolic Computation in Engineering Optimization," Engineering Optimization, Vol. 12, No. 2, Sept/Oct 1987, pp. 117-135
[10] Poli, C. 2001, “Design for Manufacturing: A Structured Approach,” Elsevier, Woburn, MA.
[11] Bralla, J., 1999, Design for Manufacturability Handbook 2nd ed., McGraw-Hill, New York.
Member discussion