Design for Manufacturing: Swarf and Burr Removal
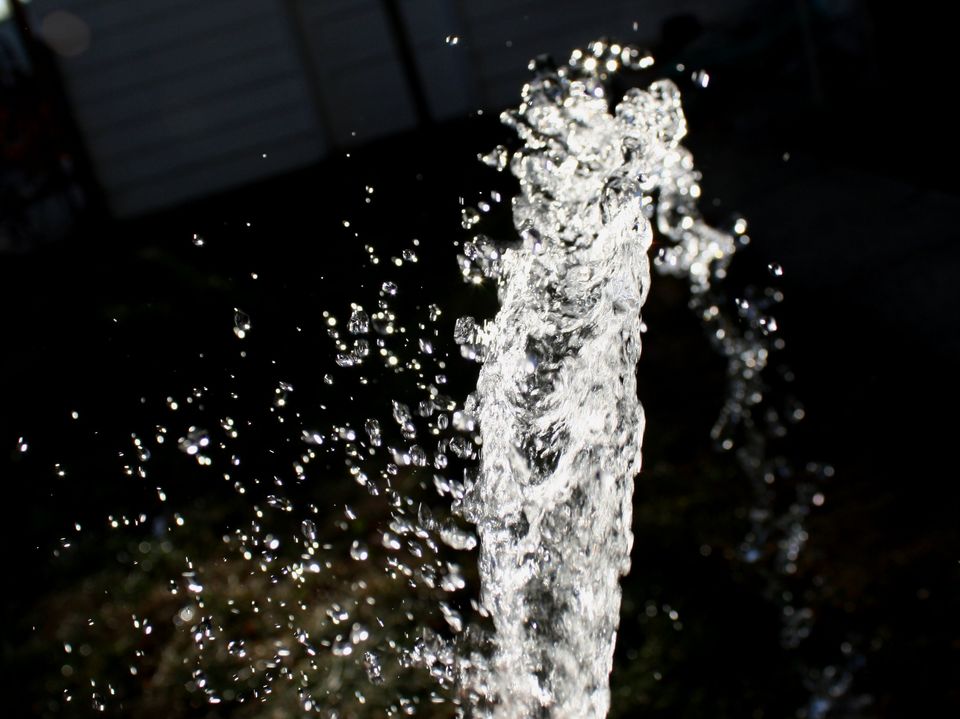
This article provides guidance on ensuring that burrs are removed from the product during the machining process. It also discusses the removal of the swarf.
Swarf is the byproduct of subtractive manufacturing processes. It may be in the form of chips, shavings, burrs, splinters, or other particulate. Swarf impedes the milling process and should be removed as soon as possible. Some higher-end milling machines incorporate automatic vacuuming as a feature of the machining process. You should ensure that tight areas are machined with the idea that debris will be removed.
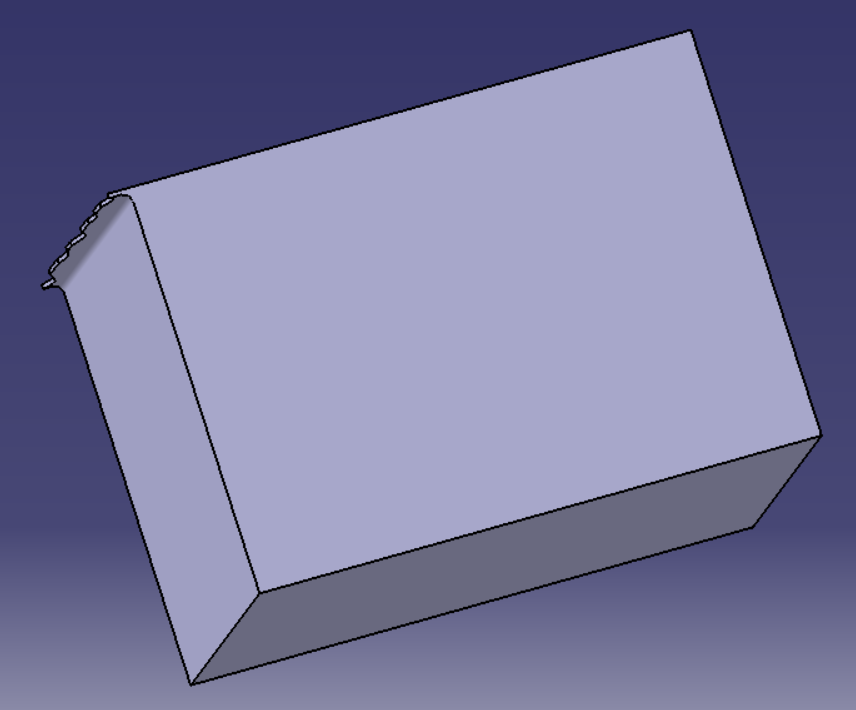
Burrs are undesirable deformations on the edges of machined parts (shown above). Burrs are extremely common and must be removed to prevent injury or damage. Burrs are commonly removed with an abrasive powder. The machined part may be subjected to barrel tumbling or abrasive jetting/sandblasting. Alternatively, high-velocity water jets may be used to smooth burrs. High-speed rotating brushes may also be used to remove burrs. Belt sanders are also an option for planar surfaces with burrs. Abrasive chemicals may be used to dissolve burrs. Electrochemical deburring may be accomplished as well. Newer processes are also being developed, such as laser ablative burr removal and plasma glow deburring.
Burr removal can cost up to half the overall cost of machining a part. Design engineers must anticipate the cost of removing burrs and factor that in when determining when that must be burr free.
Key points:
(a) Design a path for swarf removal when possible. Vacuuming or pressurized air are the preferred methods.
(b) Design parts so that burrs are allowed when possible
(c) Select materials that minimize burring when permissible
(d) Orient the part such that electrical short circuits are not possible from burring
(e) Design the part such that burrs cannot jam mechanisms
(f) Avoid tolerance stacking
(g) Relocate bosses and shoulders to avoid burrs
This article's key points will prevent product damage from edge irregularities, personnel injury due to burrs, and product failures due to mechanical binding or electrical short-circuiting. Additionally, product machining times will be reduced due to less cleaning required throughout the machining process.
Member discussion