Design for Manufacturing: Stamped Sheet Metal Spacing
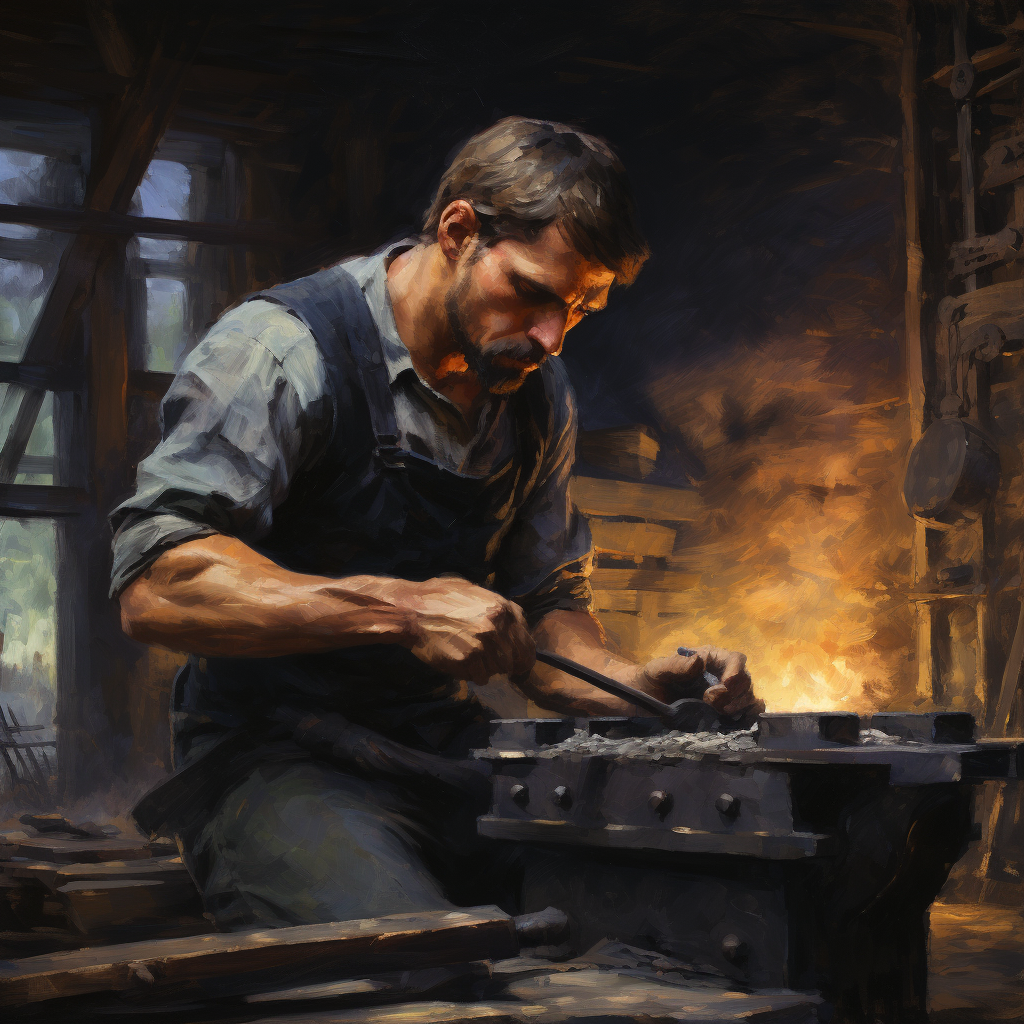
Stamped Sheet Metal Spacing:
For every feature located on stamped sheet metal, there are one or more corresponding features on the sheet metal dies. Sometimes, these features will be spaced such that there is little clearance between the original feature and other features nearby on the die. This can result in product manufacturing difficulties.
Closely spaced features are defined as those features that are non-peripheral while also being spaced less than three times the material thickness of other parts. These features add risk to the production cycle as there is a higher chance of die failure. These parts also risk product distortion due to insufficient space to clamp the part being worked. In addition, these closely spaced features add complexity to the die that may increase tooling costs.
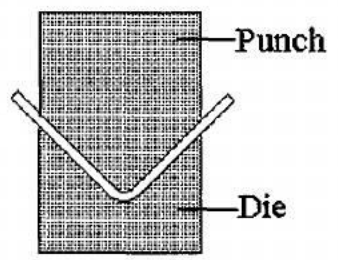
In addition, closely spaced features on the compound or secondary tooling dies are likely to have a thin section on the die block that supports the stamping. This thin section is at particular risk of breakage due to the stresses involved in the stamping process.
If closely spaced features must be used, these features must be added using a separate individual tooling station. When considering tooling costs, closely spaced features should automatically be assumed to require one additional station per set of features.
General Guidelines on Spacing:
Whenever multiple features are constrained together, the associated tolerances are also constrained together. This is known as "tolerance stacking" and can result in manufacturing non-conformances if proper care is not paid to ensure that tolerance maximums are considered. Whenever multiple features are in a tight grouping, manufacturing tolerances become especially vital to ensure that damage to the product does not occur.
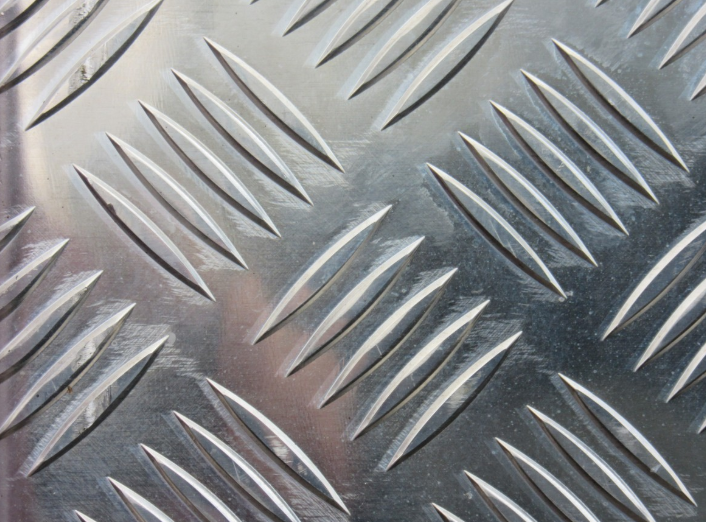
If tight part spacing is required, as in the above image, all possible attempts should be made to ensure that features are no closer than three sheet thicknesses away from each other. If this is not possible, the part may be too complex to manufacture. Alternative options are to use compound or secondary dies to accomplish manufacturing. The use of pilot holes may also help remove some variance in the manufacturing of the product.
Key Points:
(a) Ensure features are not spaced too closely together.
(b) Features should not be closer than three sheet thicknesses in distance from one another.
(c) If this cannot be accomplished, consider the use of compound or secondary dies.
(d) Closely spaced stamped parts should only be added using an additional die-stamping station
By following these guidelines, you can prevent overly restrictive tolerances that will drive up tooling and production costs. Additionally, punch breakage will be less likely to occur as there will be less metal deformation around the area to be pierced. Also, fewer die failures will occur. In addition, product distortion will be minimized as there will be sufficient clamping space during production.
Member discussion