Design for Manufacturing: Milling
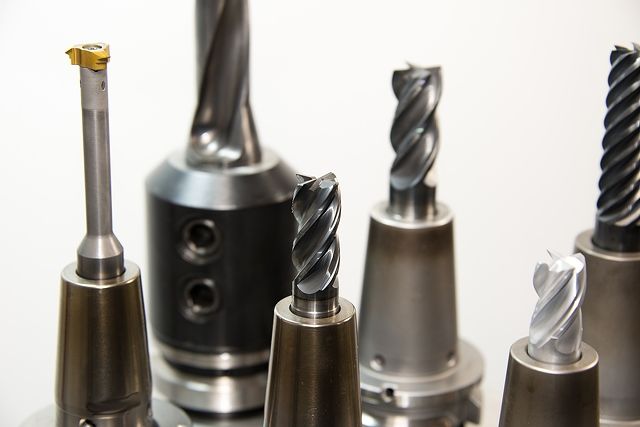
Milling is the act of subtractive manufacturing performed on a workpiece using rotary cutters to remove material. Milling is one of the most popular subtractive manufacturing techniques in use. Typically the workpiece is moved against a stationary rotating cutter that cuts a profile supplied by the operator. Cutters may act to slot workpieces, cut workpieces, chamfer, or fillet workpieces.
Milling tends to be a less expensive subtractive manufacturing method than many alternatives. Numerous styles of cutter exist that can be used to create virtually any part desired. Milling is an effective method for removing large amounts of material from a workpiece economically.
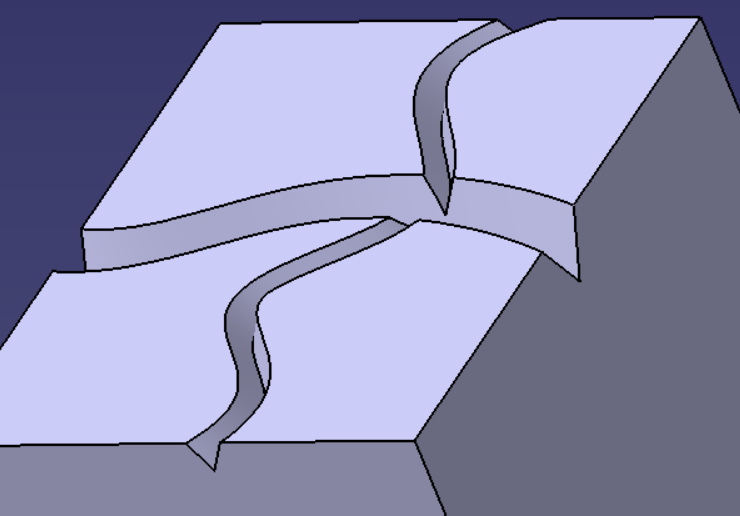
Milling should be accomplished using standard-sized cutters whenever possible. Non-standard cutters typically incur substantial reoccurring costs as cutters must be frequently replaced. If cutters must be ground down to accommodate the design requirements, this adds significant time to the manufacturing setup time.
Generally, the size of the cutter should not be specified. The manufacturer should be capable of meeting design intent utilizing available cutters. For example, a larger cutter with a shorter plunge depth may be used instead of a smaller cutter with a longer plunge depth. This ensures that tooling costs are reduced.
Key points:
(a) Use milling to accomplish feature creation
(b) Only use standard cutters
(c) If a design requires surface features or profile features, avoid the use of non-standard slot widths, fillet radii, non-standard chamfering, and corners
(d) Allow for standard cutters to be selected by the manufacturer when possible when milled surfaces intersect
Following this article can prevent costly rework from poorly machined surfaces. Additionally, you can reduce tooling costs by requiring new tooling to be fabricated or purchased.
Member discussion