Design for Manufacturing: Hole Machining
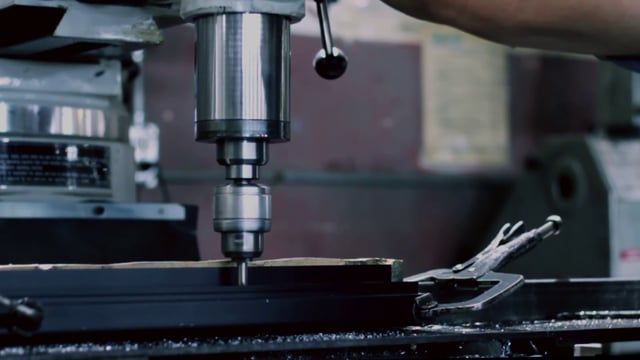
This article considers cost avoidance techniques in blind hole drilling.
Drilling uses cutters to subtract material to achieve cylindrical pockets in a workpiece. Drills typically have an angled cutter tip to facilitate material removal. The actual removal of the material is drastically facilitated by utilizing through holes instead of blind holes. This allows for chips created in subsequent operations (such as reaming and tapping) to fall through instead of being removed by vacuuming or air pressure. This not only reduces cleaning steps. Through-hole usage also reduces the chance of mechanical binding from excessive particulate buildup during drilling operations.
As drills typically use angled cutters, the question of the desired shape of the hole tip can be best resolved by maintaining the angle the same as that of the cutter. Specifying square-bottomed holes forces machinists to perform additional steps to flatten out the bottom of the hole. Additionally, subsequent reaming operations place the machinist at a distinct disadvantage concerning chip removal from the reaming process, as there is no clearance for chips to collect under the reamer. Ultimately, there are few circumstances where a flat-bottomed hole is required to meet design intent.
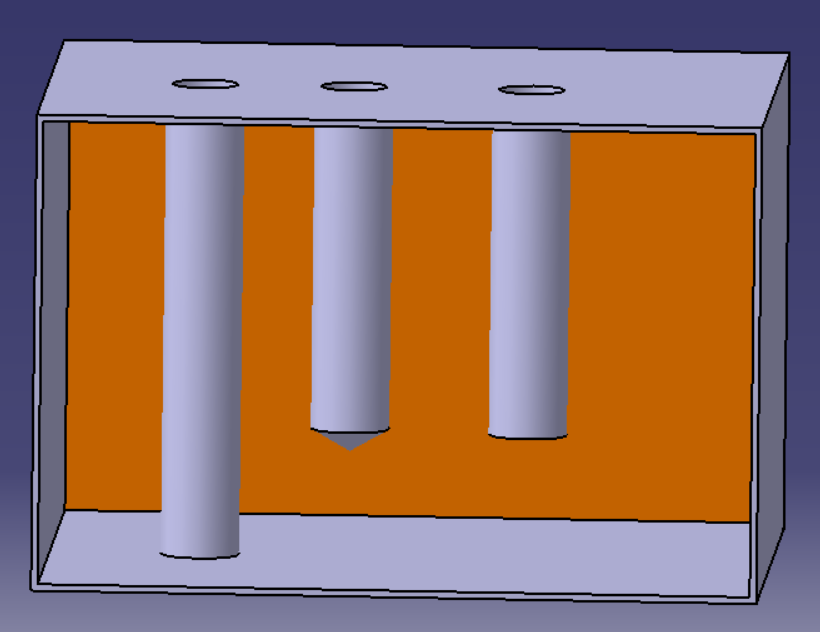
Key points:
(a) Avoid the use of flat-bottomed holes to minimize subsequent drilling operations
(b) Avoid using flat-bottomed holes when reaming operations are to be performed.
(c) Preferentially design machining operations for through-holes instead of blind holes whenever possible.
Use of what we covered in this article will minimize the number of operations required to produce holes in machined parts. This drives tooling costs and machining costs down.
Member discussion