Design for Manufacturing: Drilling Surface Requirements
This article considers the requirements for drilling surfaces in the context of minimizing manufacturing flow times and costs.
Drill entry and exit criteria are of particular concern to design engineers creating parts and products.
Drill entry surfaces should be perpendicular to the drill when at all possible.
Not obeying this rule will result in the drill skipping across the surface to be drilled at a drastically increased frequency. This will result in part damage in addition to wearing out the cutter faster.
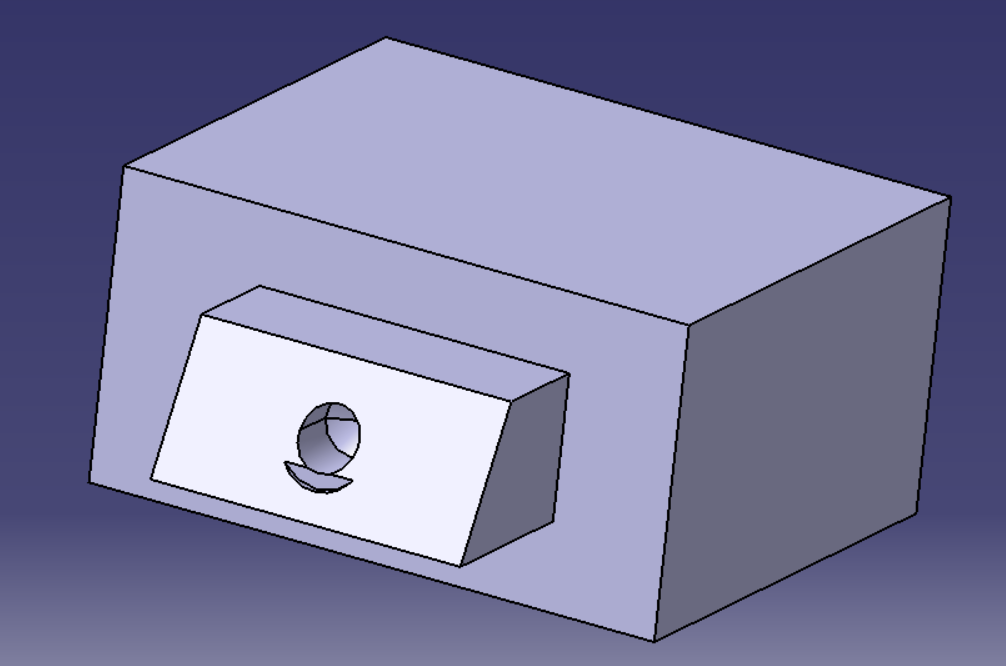
Additionally, the drill cutter is much more likely to start cutting in the incorrect location when a non-perpendicular angle of attack is used. This usually results in part rejection, as correcting this problem is unlikely without expensive rework.
Similarly, exit surfaces should always be perpendicular to the drill as well. Failure to perform this design rule will result in the cutter potentially fracturing the area around the exit surface. This is due to high localized stresses due to the extremely small area of cutter force application on the edges of the hole being cut. Without performing this step, the cutter can skip along the edge of the work surface and mar it unnecessarily.
If
(a) While designing parts to be drilled:
(b) If the part has angled surfaces
Then
(a) Do not place drill entry points at an angle to the face to be drilled.
(b) Do not allow for drills to exit at non-perpendicular angles.
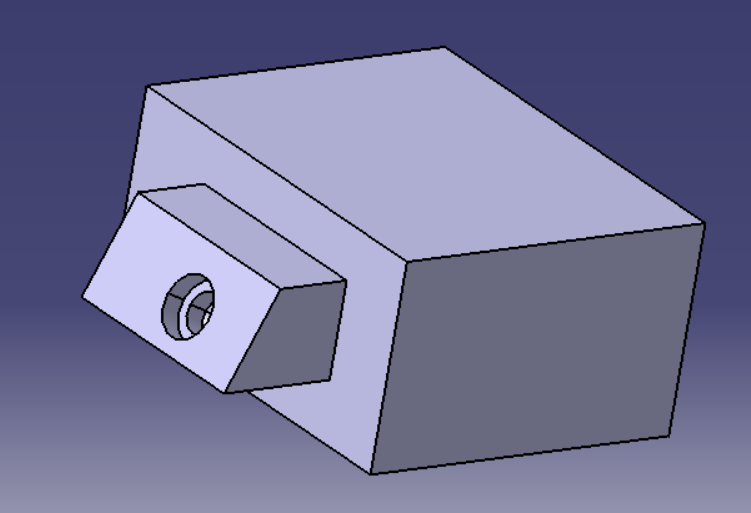
This rule will prevent tool skipping, tool breakage, and part damage. Tool skipping and breakage reduction will reduce tooling costs over time. Reducing part damage allows for a faster part production rate due to fewer rejection losses while minimizing costs.
Member discussion