Design for Manufacturing: Drilling
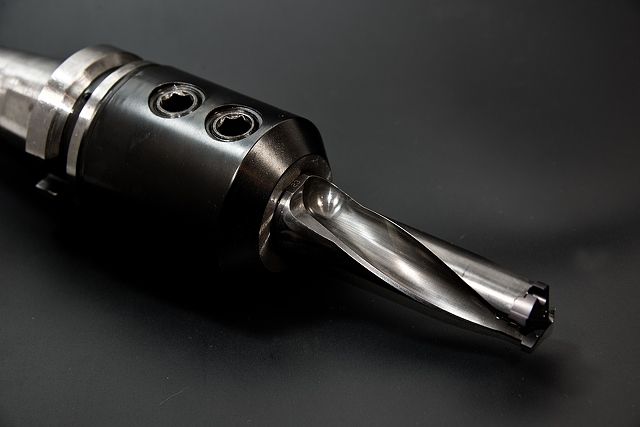
This article discusses the economics of drilling operations regarding what to use and when.
Drilling is the process by which a round hole is produced by a rotating tool. This encompasses the processes of drilling, reaming, and boring. Drilling and boring are particularly interesting for design engineers seeking to reduce costs as these operations may make up a significant amount of the manufacturing cost.
Boring is the process where an existing pilot hole is enlarged by removing metal using a rigidly mounted cutting tool. Boring does not involve depth changes; instead, it is the process by which hole diameter and finish are altered to meet engineering design intent. When precision or a high-quality finish is required, boring is the solution that should be utilized.
Whenever high production runs are in progress that involves drilling, consideration should be made for the method by which the drilling will be accomplished. Using multiple spindles to perform drilling allows for cutting various surfaces at once. As this drastically reduces manufacturing times, the added cost is justified. Otherwise, consider the use of vertical milling machines for low-quantity work.
Key points:
(a) For high production levels of approximately 10,000 units per year, use multiple spindle drills
(b) Otherwise, use single spindle drills in production.
(c) For low-quantity work, vertical milling machines are likely the most cost-effective machining method.
(d) When exceptional accuracy must be maintained with regard to hole diameter, placement, straightness, or direction, make use of boring machines
Following these several vital points will ensure the most efficient drilling process, and style is used. This will reduce manufacturing time and costs associated with producing the feature.
Member discussion