Design for Manufacturing: Curling and Hemming Sheet Metal
Curls are features produced by rolling the edge of a stamped sheet metal part. These curls should generally have a diameter of about 10 to 20 times the thickness of the material being worked. Curls are produced to shape the material into a hollow ring. This is typically done to eliminate sharp edges. In some situations, these curls are used as hinge features.
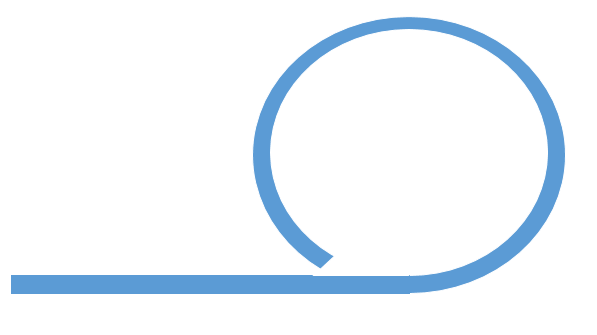
Curls may also be used to increase the stiffness of the product. This is accomplished by increasing the moment of inertia at the ends. Curls may also act as stiffeners at the edges by increasing the effective thickness at the ends.
Curls are similar to hems. Hems are used for the same purpose as curls; however, their formation is slightly different. Hems are curls with a diameter often approaching zero. Hems are produced like curls, except they are flattened at the last step.
Key Points:
(a) Curl diameter should be 10 to 20 times the thickness of the material stock.
(b) The sheet metal should be notched before starting a curl or hem operation.
(c) A wiping operation should generally precede curl or hem operations.
(d) Three total operations per curl or hem feature should be required. Hems will be flattened following creation.
Following these key points ensures that curls and hems are satisfactorily formed. Otherwise, your sheet metal will not have proper rigidity.
Member discussion