Computer-Aided Fixture Design
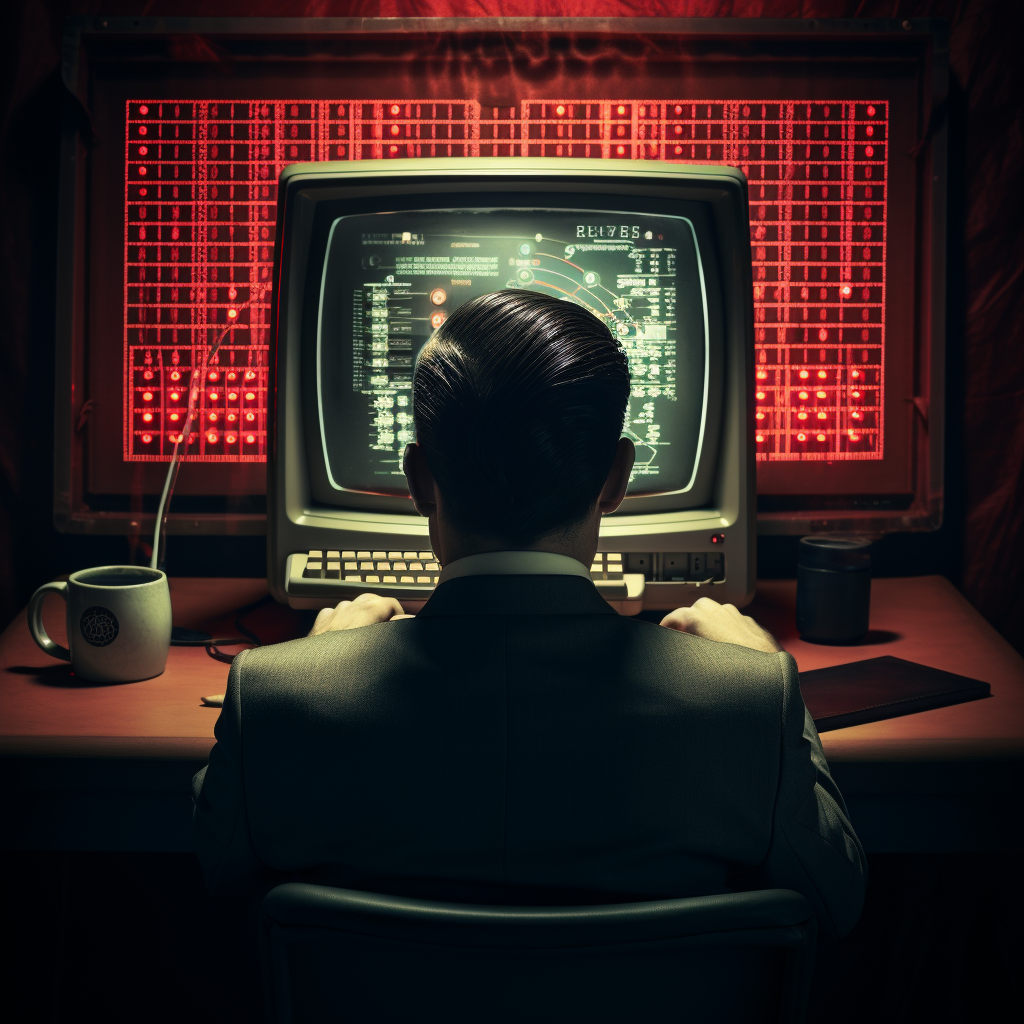
The development of computer-aided fixture design (CAFD) can be traced back to three primary stages of consideration. The first stage is the problem definition (PD) phase. The next stage is the fixture synthesis (FS) phase. The final stage is the fixture analysis (FA) stage. A practical, efficient fixturing solution can be developed by utilizing a set of processes at each stage.
Problem definition can be described as understanding the fixturing problem and enumerating the design variables, system constraints, and solution criteria. Design variables typically include fixturing elements, fixture assembly options, equipment sizes, and the force required to be applied to the product to achieve the desired result. Design constraints include the method of attaching the fixture to the product, accessibility of the fixture for the assembly worker, and the stress required to be supported by the fixture. Design criteria can be summarized as the total budget to be applied to the fixture, the skill required of the assembly worker to use the fixture, the production rate required on a per-fixture basis, and the needed overall quality of the fixture. As this step drives the remaining two steps, it can be the most important.
Fixture synthesis concerns itself with the design variables of a given fixture as required to meet design constraints. This requires selecting the subassemblies and parts that will make up the fixture. In addition, clamping positions and methods must be determined. Support and locating points will also be chosen and configured in this step. Finally, the overall assembly of the fixture will be decided. One major point of consideration is that the method of fixture synthesis used will drive the amount of design accomplished by CAFD in this step.
Fixture analysis evaluates the fixture to verify that design criteria are met. During this stage, several tools may be used to ensure that constraints are not breached, and the fixture will function appropriately. Kinematic analysis may be used to validate that movement, and accessibility are acceptable. Force analysis may be used to ensure that the fixture is well-balanced and will not tip over. Finite element analysis may be used to check for overstressed points to prevent fixture or product deformation.
Pehlivan and Summers [1] discuss the different individual inputs and outputs for each stage of fixture development. Numerous algorithms and tools are in active use for problem statement elaboration, fixture synthesis, and fixture analysis. Some of the more exotic methods used are genetics-inspired planar geometry algorithms that are then analyzed using finite element methods and heuristics algorithms, which assist in determining fixture stability. Most analysis methods involve geometric analysis; however, not all do. Many use programming environments to drive toward a solution iteratively. Ultimately, it is the design engineer's responsibility to pick the systems that will produce the overall best value-added fixture for the problem statement requirements.
References:
[1] Pehlivan, S., Summers, J., (2008), "A Review of Computer-Aided Fixture Design with Respect to Information Support Requirements," International Journal of Production Research, vol. 46, no. 4, pp. 929-47. (DOI: 10.1080/00207540600865386)
Member discussion