Direct Metal Laser Sintering
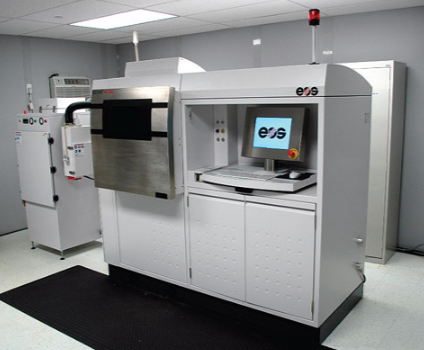
In direct metal laser sintering, metal powder is placed on a print bed by an automatic powder-layering blade. This blade spreads powder evenly across the print bed, typically at a depth of about 20 micrometers. The print bed generally is preheated to minimize the warping of the printed material from uneven cooling of each layer.
A laser (typically CO2, Nd: YAG, fiber, or disc lasers) is then beamed across various points on the print bed to fuse the powder into a solid form. Rather than using a laser to cure photo-reactive resins, as in stereo-lithography, the laser directly deposits energy on powder to partially melt it. The print bed lowers by a value corresponding to the desired layer height. The automatic wiper blade spreads new powder across the top layer of the solidified powder, and the process repeats itself until the part is fully formed.
Laser selection is critical in the design of a part and the selection of the exact characteristics the product will have. The laser wavelength will have a significant impact on the absorptivity of the selected powder. Depending on the desired microstructure formation, a given laser and powder pair should be chosen to accomplish the design intent of the part.
Additionally, the maximum power of the laser must be considered before selection. The laser's power rating determines the beam's overall energy density possible. Energy density drives the overall metallurgical phase change that the powder will undergo. Specific material properties may be required by the design, and, as a result, a particular set of laser output energy levels must be included in the toolpath code.
Each layer of a DMLS part typically sees about 25 ms of laser exposure. This short thermal cycle prevents any sintering process other than liquid phase sintering from being possible. Liquid phase sintering partially melts each powder layer and then allows it to solidify. This is accomplished under an inert gas blanket to minimize oxygen concentrations available at the sintering location.
DMLS powder makes use of three primary components. The structural metal that makes up the bulk of the part typically has the highest melting point. This allows for maintaining a primarily solid core within a liquid filler material. The filler material has a low melting temperature, so it may act as a binder between particles of the structural metal.
Finally, chemical additives are added to the mix to allow for the introduction of flux and deoxidizing agents. Flux is a cleaning agent to prevent chemical impurities from being introduced into the end product. Deoxidizing agents prevent oxygen introduction into the metal, which will result in a lower-strength product being created.
Future research in direct metal laser sintering focuses on alloy material optimization. In keeping with typical metallurgical concerns, alloys have individual melting temperatures for each constituent metal. The same research that went into determining the best method for smelting a bar of a given alloy must also determine the exact characteristics that result in an ideal microstructure formation for a given alloy. This research is complicated by the quick thermal cycling time due to using a high-powered laser rather than a furnace.
As a result of suffering from a non-congruent melting point, alloy powders undergo a slurry phase between the solidus and liquidus temperatures. This slurry phase is desirable as it promotes the wetting of still-solid particulate and grain boundaries of non-melted metals. As a result of this wetting, capillary forces allow for the rearrangement of particles such that the net strength of the material is improved.
Current technology requires the post-processing of direct metal laser-sintered parts. This takes the form of hot isostatic pressing, post-sintering furnace work, and secondary infiltration of low melting point materials. Through better optimization of the sintering temperature and overall thermal cycle, these post-processing steps may be reduced or eliminated in future DMLS systems. This will result in both cost and time savings for the manufacturer.
Laser sintering provides relatively high product stability with many materials available for use. Any material which can be made into a powder may be sintered, which results in extraordinary flexibility in material selection. Due to the nature of laser sintering, no support structure is required, significantly reducing build time and complexity. Additionally, only minimal post-processing is required compared to many other additive manufacturing systems.
Laser sintering suffers from both a high power consumption rate and typically requires a large footprint to place the machinery. Laser sintering also produces a poor surface finish due to the large particulate size. Laser sintering results are also highly dependent on the powder quality for the sintering action to occur.
References:
Gu D., Meiners, W., Wissenbach, K., 2012, "Laser Additive Manufacturing of Metallic Components: Materials, Processes, and Mechanisms," International Materials Reviews, 57:3, 133-164.
Chua, C., Leong, K., 2015, 3D Printing and Additive Manufacturing Principles and Applications, World Scientific, New Jersey, USA.
Member discussion